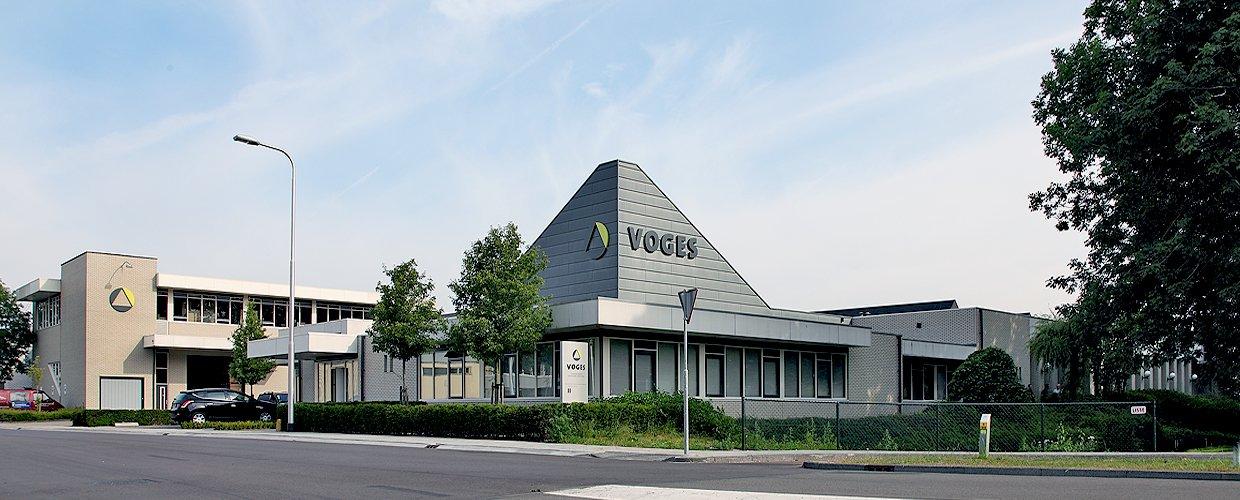
Voges Performs.
Since 1882.
Voges has been trading since 1882 and traces its origins to the export of bulbs. Our founder John Voges noticed early on that using high-quality packaging was crucial for delivering bulbs.
Just in time.All the time.
Just in time was already a major issue back then, when transportation took longer than it does today. When the company moved into the mail order business in the 1920s, the demand for high-quality packaging became even bigger.
Dissatisfied with the levels of quality available at the time, Voges decided to set up his own range of packaging. And it was a great success. By applying innovative solutions, Voges was able to significantly reduce packaging costs, whilst increasing the quality at delivery.
In the 1970s, Voges completed the move to plastic packaging. And today, the current owner, Albert Voges, specialises in developing packaging and in-house packaging design, continuing the company's work towards the best-performing packaging.
We provide plastic packaging for various markets. We originally began supplying the horticultural sector. Over the years, businesses in the sectors of consumer goods, food products, health & beauty and electronics have come to us too. We have a packaging solution to suit virtually every market.
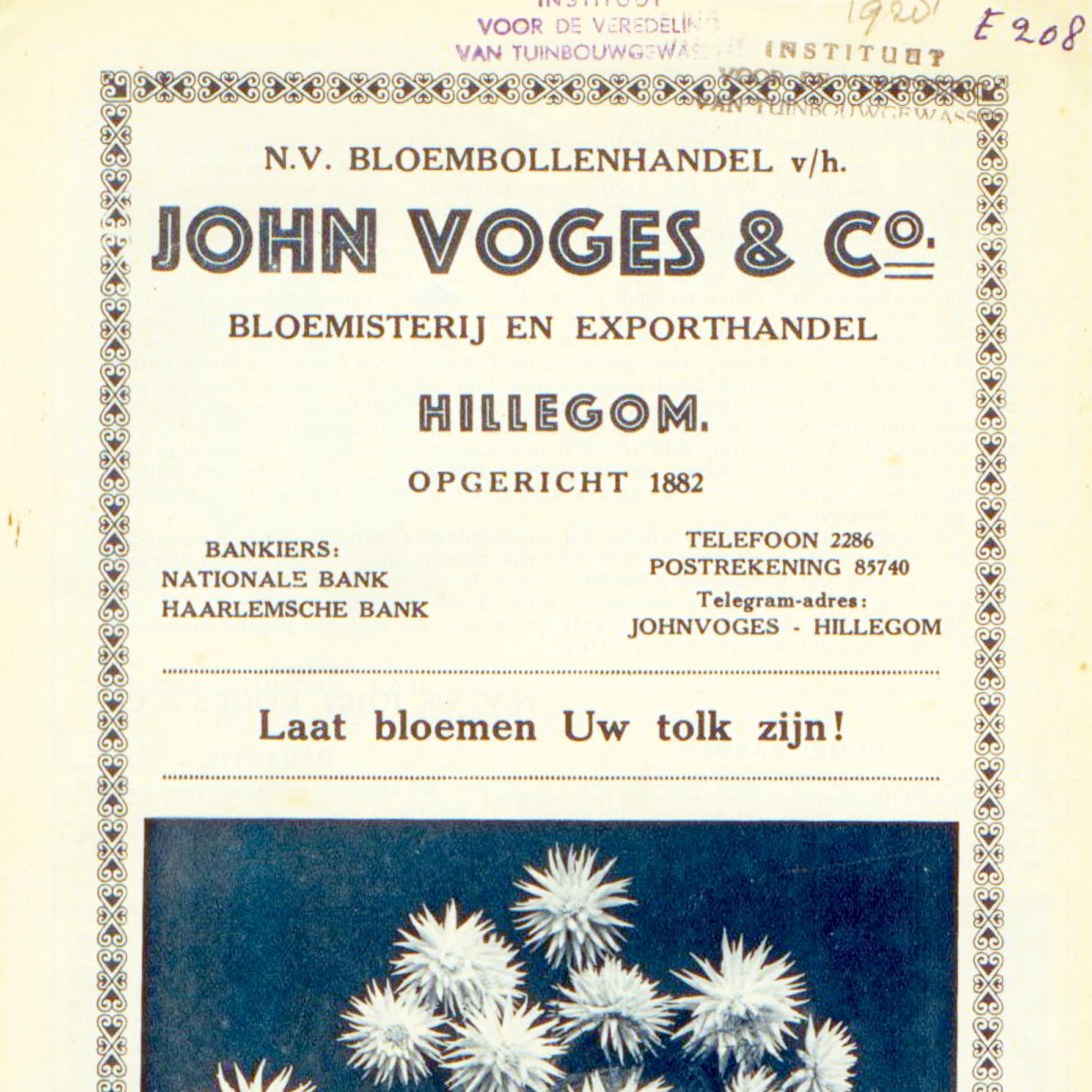
From the ideato the packaging.
We design the moulds for your packaging in-house in our own studio. That way you can rest assured of getting the packaging solution to exactly suit your needs. From a complex, tailor-made item to simple applications, we are happy to come up with a solution for you and will swiftly produce a concept and a trial model.
At Voges we make sure that your plastic packaging needs are all met in one go. A one stop shop, from the idea to the packaging. In order to guarantee our high levels of quality, we follow an established project phasing structure. That also means you can be assured of reliable delivery.
The production process for our thermoformed plastic packaging is made up of the following steps.
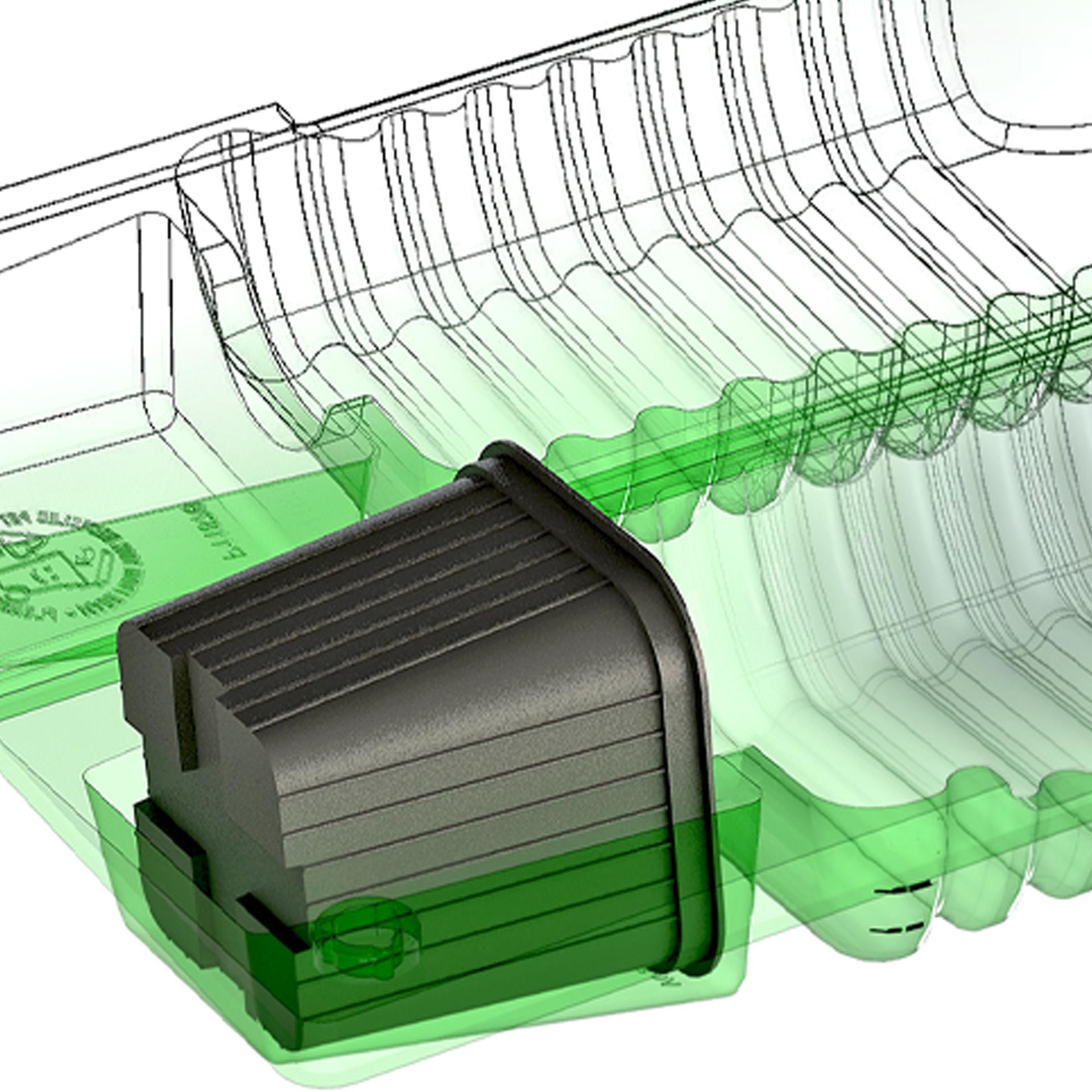
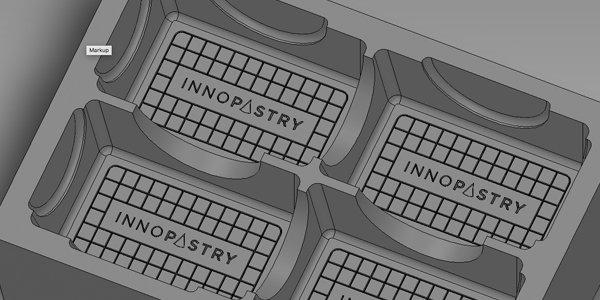
1. Design
Your preferences and requirements are fully set out in an explanatory talk in which we explain our innovative solutions and technological advances in the market. We then design your packaging in 3D, using our CAD system.
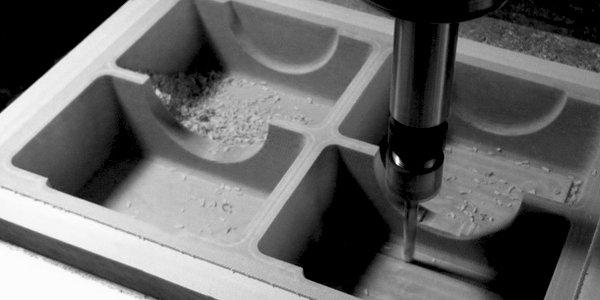
2. Trial Model
We calculate the cutting paths based on the 3D drawing in our own studio. We use a CNC milling machine to make a trial mould, which then quickly produces a trial model. You can then present this internally. We will then implement any changes that are made, to give you a clear picture of the final result. Finally, we work towards a final production design.
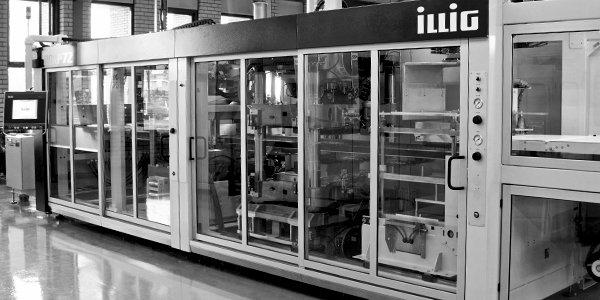
3. Production
After the design phase has been completed, the vacuum-formed plastic packaging is manufactured as follows: We feed a strip of plastic into the machine, and make the material flexible by heating it. Once it has been heated, we put the flexible material into the mould. Once the material is in the mould, it is prestretched with a stamp, whilst a vacuum pulls it from the other side. This technique puts the packaging under pressure from above and below, and this pressure from both parts of the mould produces the desired shape. Our hole-punching equipment and cutting template ensure each piece of packaging is neatly finished.
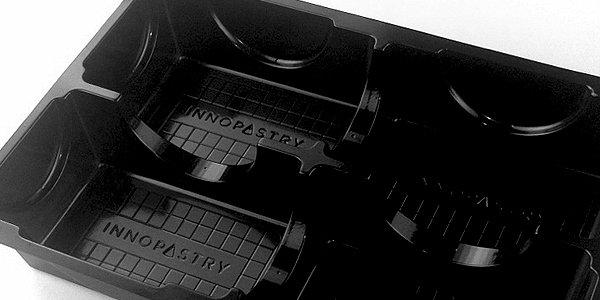
4. Logistics & Aftersales
If you wish, we will deliver the whole order to your packaging site and will help think about your Just in Time process. The world of plastic packaging never stops moving, and neither do we. After we have delivered your packaging order, we will keep you up to date on new solutions and options emerging in the world of packaging. So that the next time you place an order you know that your packaging will perform in live with the latest norms.
Sustainable Capacity.All Solar Powered.
In our workshop, 14 ILLIG machines ensure consistent capacity for vacuum-formed packaging, accommodating up to a maximum area of 75 x 53 cm. With our own moulds and a stock of plastics, we can swiftly respond to a variety of orders.
Our commitment to sustainability is unwavering. We recycle materials and reuse processing water throughout the production process. We minimize energy consumption across the production lifecycle and continually invest in state-of-the-art technology, generating all the energy we use with solar panels.
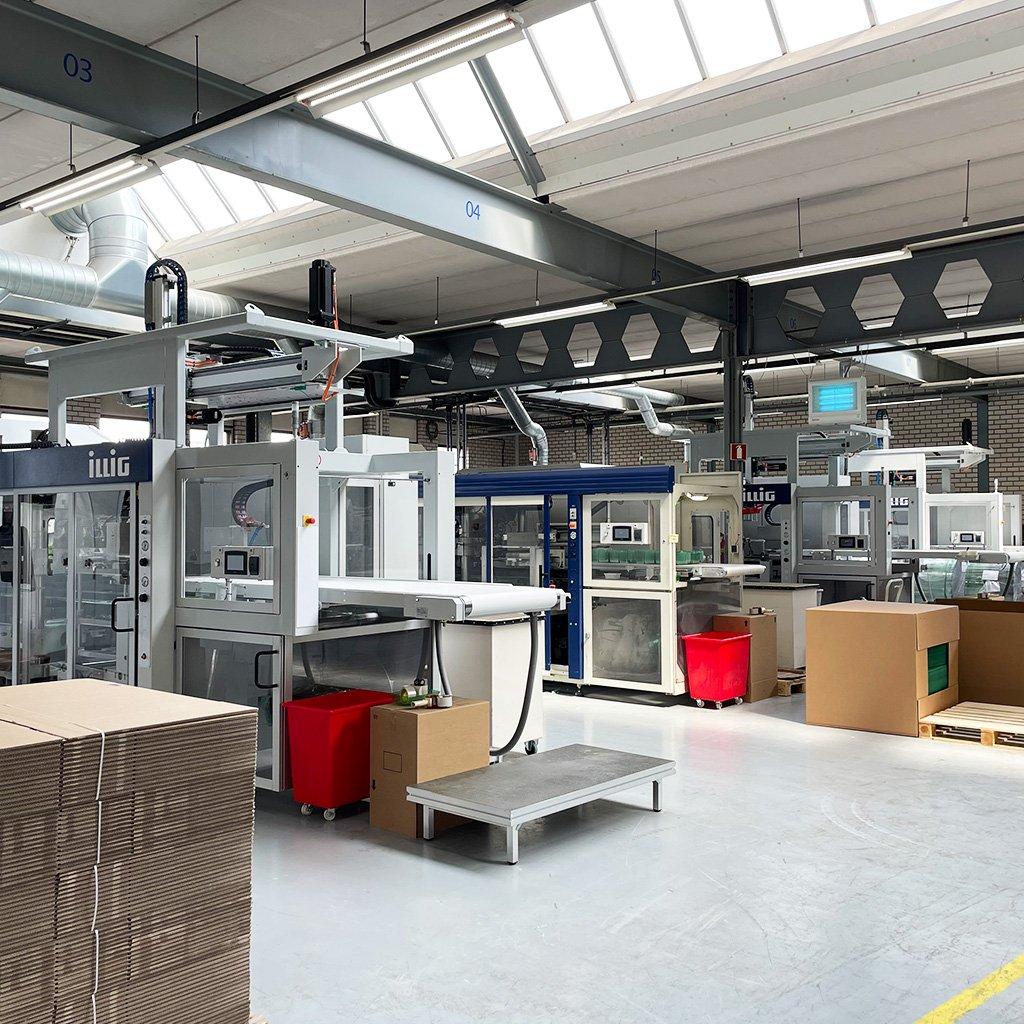