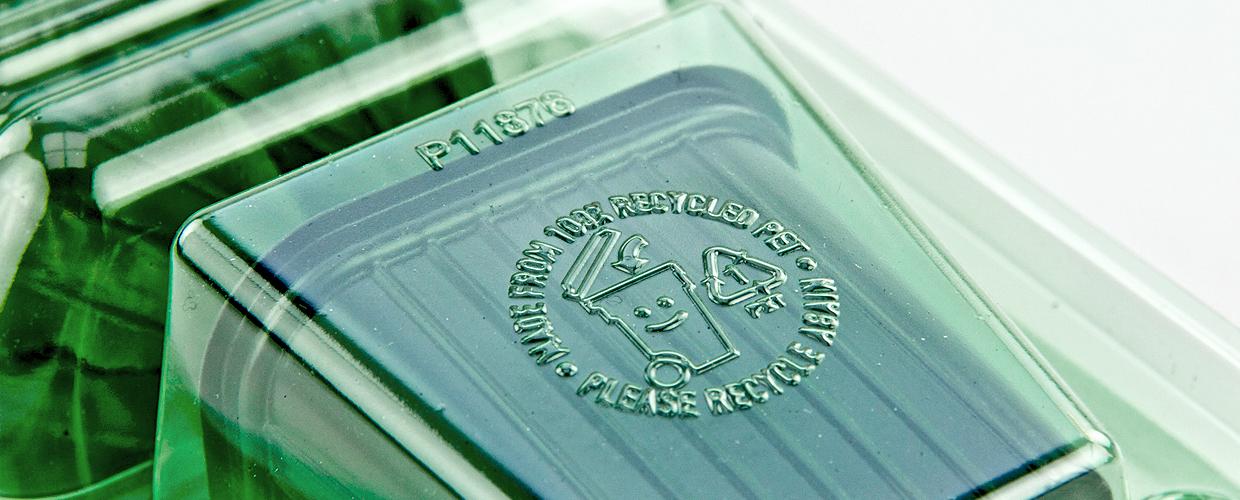
Plastic.
The sustainable choice.
Voges designs and produces specialized plastic packaging for growers and retailers to deliver and ship plants. We've deliberately chosen plastic because, compared to other materials, our use of it has a minimal environmental impact.
Plant packaging. TNO recommends plastic.
When it comes to plant distribution, cardboard may have a green reputation with consumers, but TNO's thorough research tells a different story. Plastic packaging actually comes out on top. Across the whole product cycle, plastic, especially rPET packaging, boasts a 20% to 30% lower environmental impact compared to cardboard.
Have a look at the full TNO research report 8610/U93.
How plastic comes out ahead:
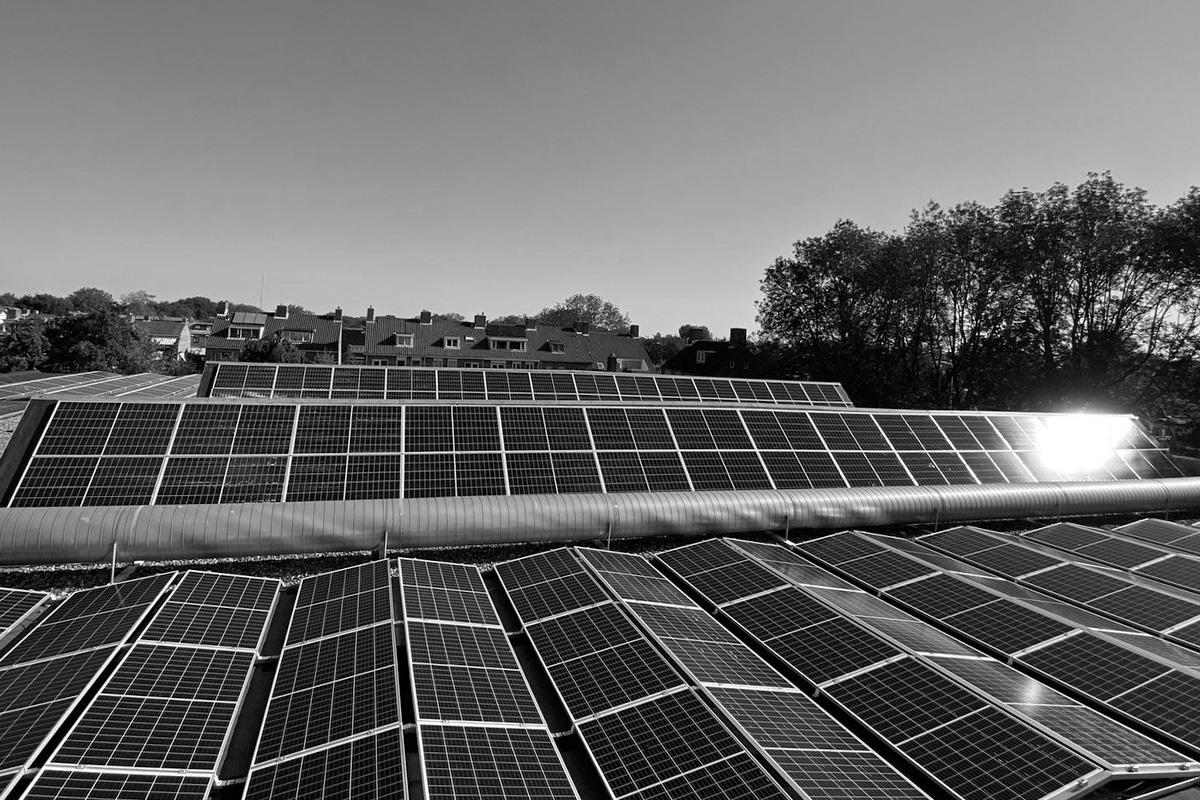
Less energy.
rPET packaging consuming up to four times less energy. Electrical and thermal combined.
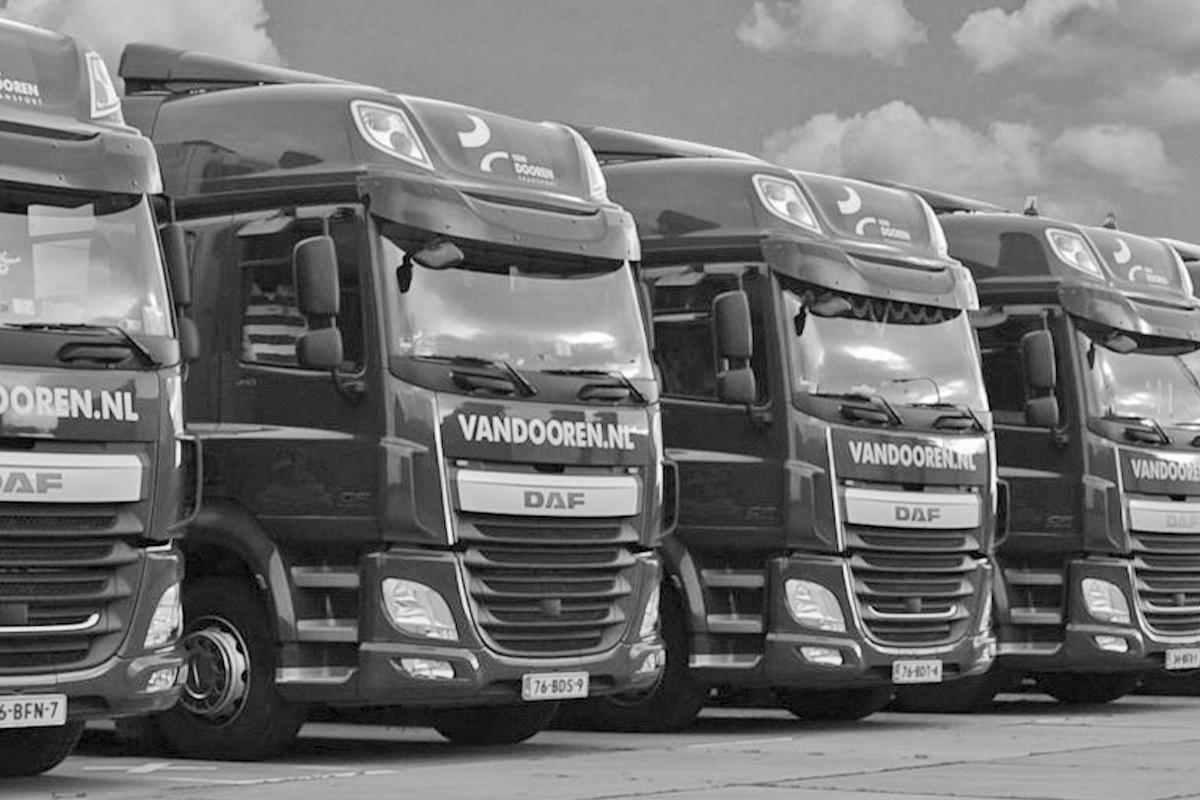
Logistics. Optimized.
rPET packaging consuming β¨up to seven times less space. One truckload instead of seven.
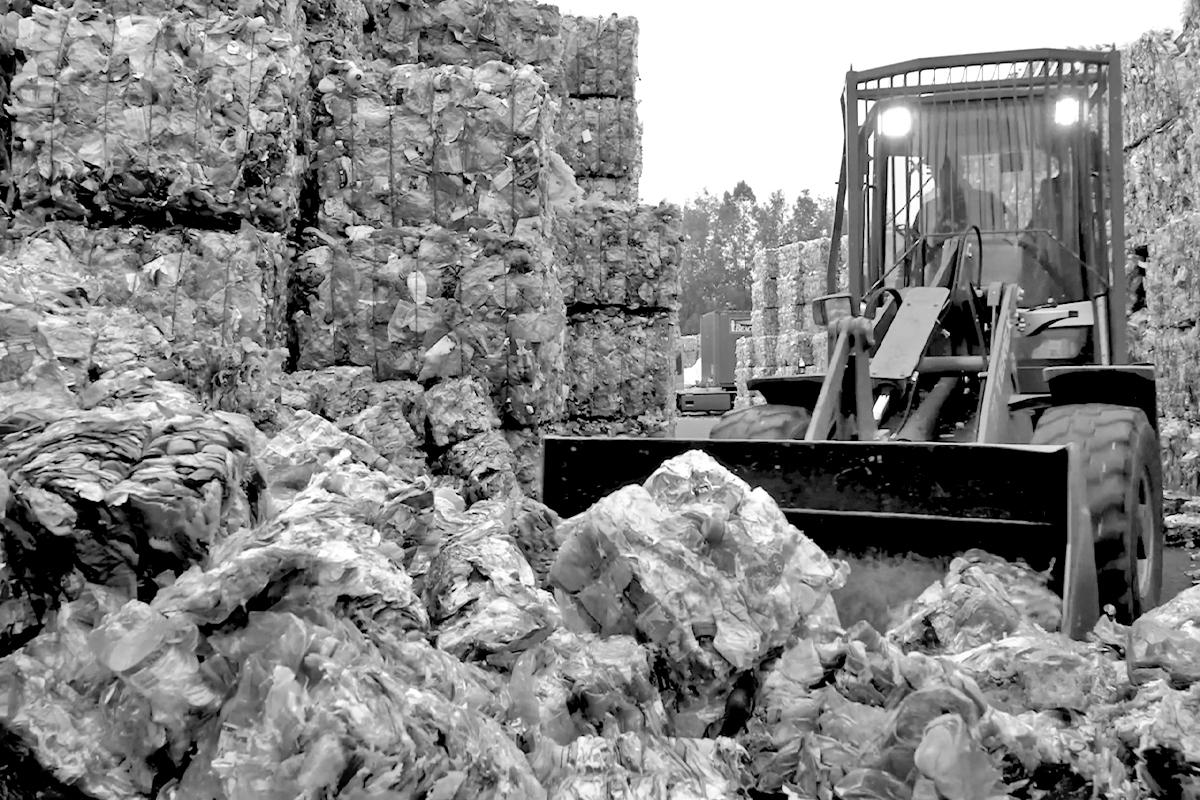
Less waste.
rPET packaging produces significantly less emissions β¨into water and air.
Look at the comparison.
rPET packaging vs Cardboard packaging.
Plastic is ultra-thin, lightweight and moisture-resistant.
Less weight means lower transportation costs and less environmental impact. Ultra-thin packaging that provides excellent protection and is moisture-resistant? It's possible with plastic.
Better Use of Space.
Cardboard occupies up to seven times more space, affecting storage and transportation requirements for stacked or packaged products.
Reduced Raw Material Weight.
To make cardboard or plastic, you need raw materials. Plastic requires over three times less raw material weight compared to cardboard. This difference has a significant impact across the entire supply chain.
Our approach.
Reduce & Recycle.
The TNO report provides a clear picture. Yet Voges does not ignore the challenges posed by plastic. This perspective guides our design and production philosophy, emphasizing reduction and reuse of plastic.
We reduce by
π Maximizing plant life by using strong moisture-resistant packaging that allows light to permeate;
π Minimizing energy consumption throughout the production lifecycle and continually investing in state-of-the-art technology; Generating all the energy we use using solar panels.
π Designing lightweight packaging (the less plastic, the better); The lighter weight enables lower transport costs and reduces the burden on the environment;
π Optimizing logistics through compact boxing and the efficient distribution of packaging;
We recycle by
π Committing to rPET made of mono-plastic as this is most suitable for recycling purposes;
π Aiming for Zero waste. If you work with plastic there will be plastic waste. Everything that is left - each and every bit of it - is collected by us and offered to our recycled PET plastic producer for reuse;
π To encourage buyers to recycle and separate their plastic waste, we emphasize this commitment by making the recycling logo larger than our own logo.
Recycling last longest.
Join in.
Are you looking for the most sustainable packaging material to transport plants? While plastic may contribute to a growing problem, when managed properly, it can be part of the solution. Recycling remains a crucial part of that solution.
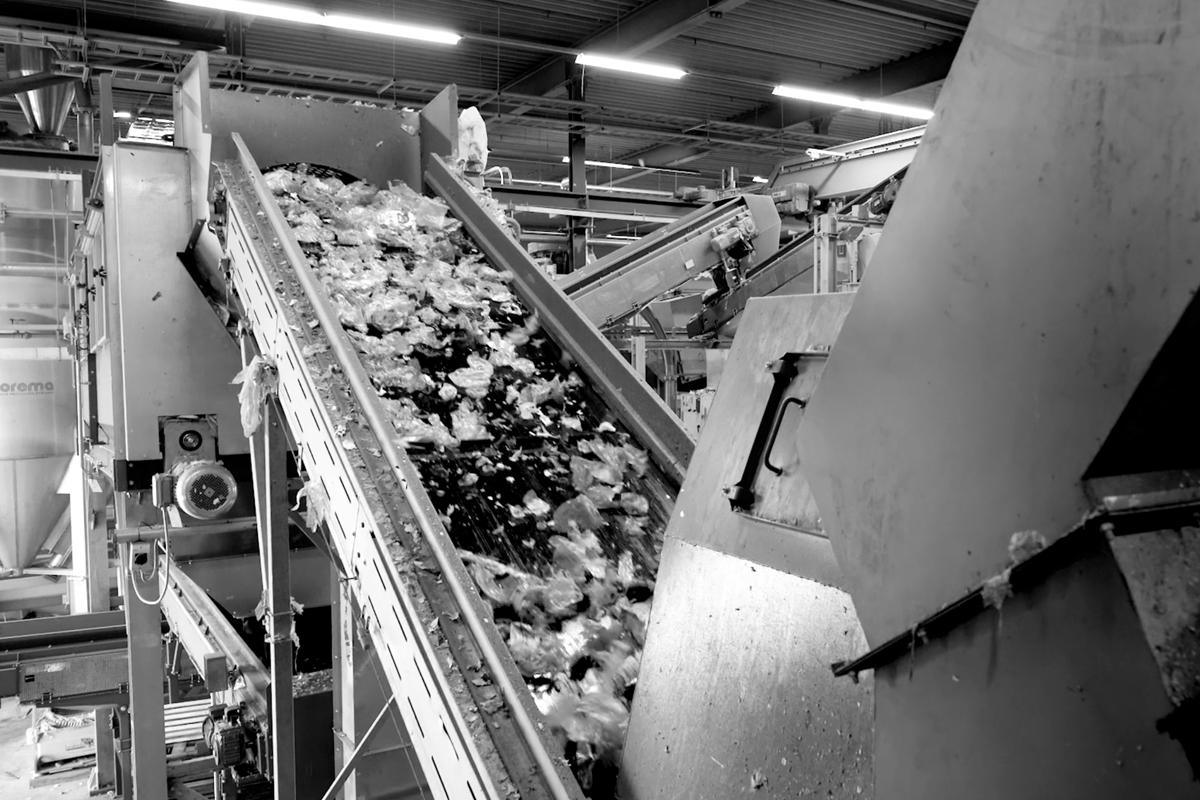
What our suppliers do.
Our suppliers process tons of Post Consumer Waste a day. Old packaging is simply used to make new packaging.
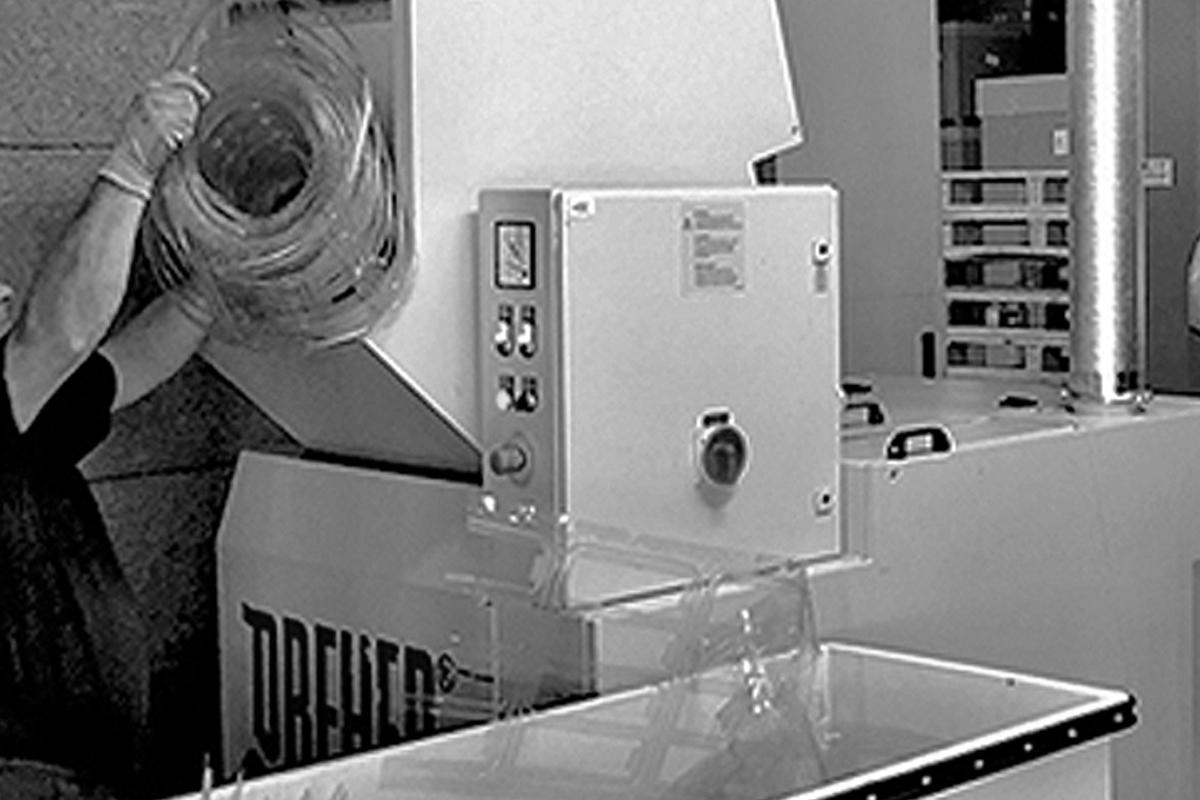
What we do.
If you work with plastic there will be plastic waste. Everything that is left - each and every bit of it - is collected by us and offered to our suppliers for reuse.
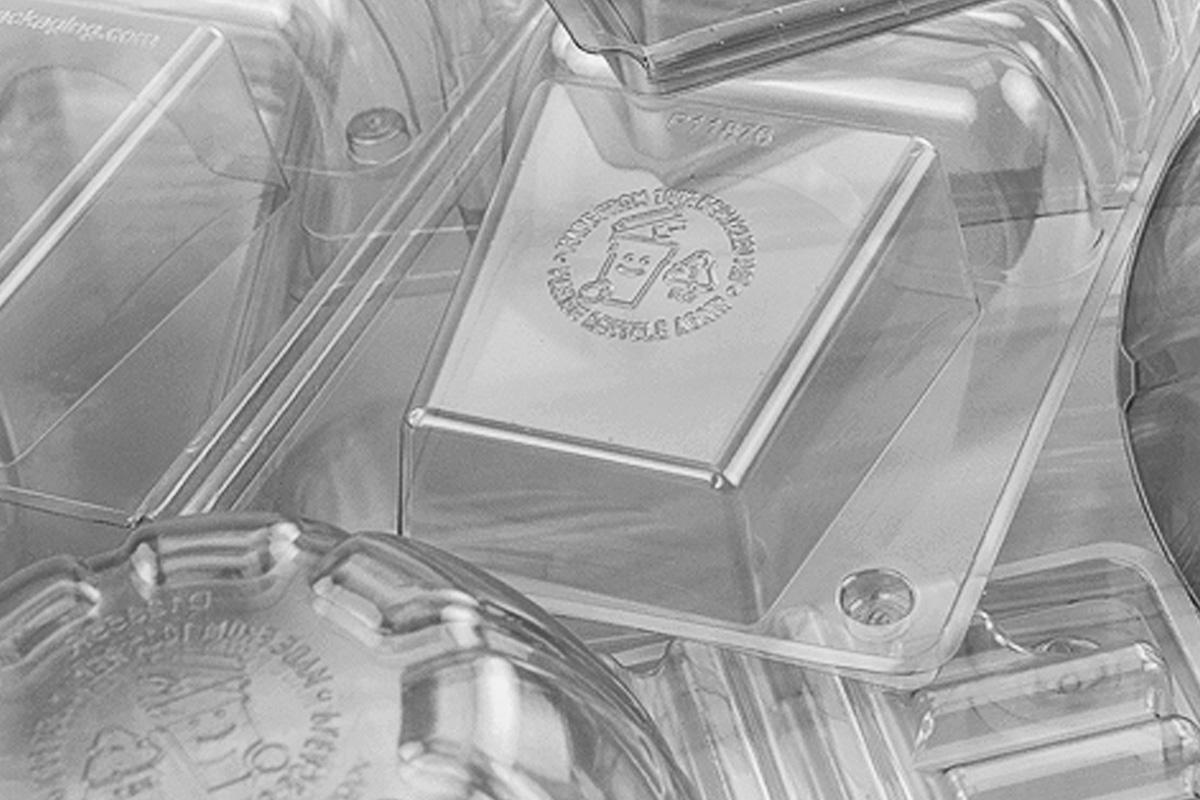
What end users do.
Our packaging users often have green fingers, leading by example when it comes to sustainability. They actively separate plastic for recycling and deliver it back to our suppliers, helping to close the loop on waste management.
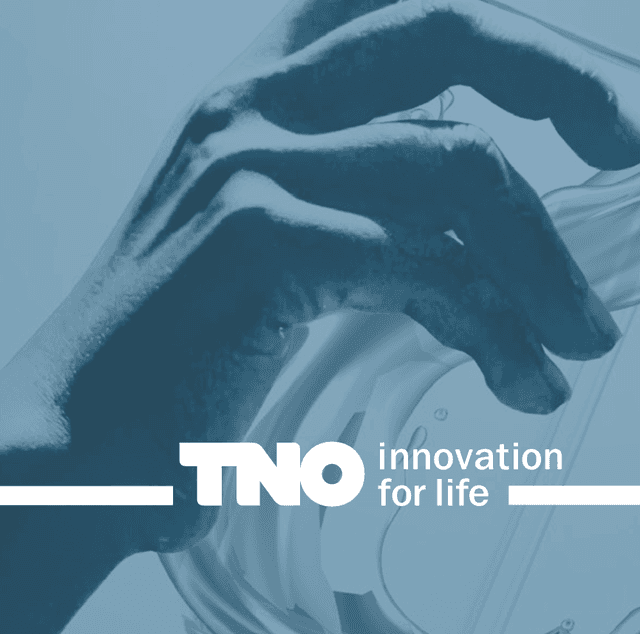
Plastic is the better option when it comes to packaging plants. When you take the entire lifecycle into account, plastic outperforms cardboard by a long way.
Bioplastics.
A beautiful promise.
We manufactured a complete range on the basis of Ingeoβ’ biopolymers as early as 2003. This so-called performance plastic uses corn as a renewable raw material. This type of packaging is 100% degradable.
Today, however, it is more of a fine promise than an effective solution.
On the one hand this is because the packaging nearly always ends up with other plastic waste to be either processed or burnt, and on the other hand because there is insufficient availability in the market to meet the current demand.
Want to know more? Read this article from the Plastic Pollution Coalition: Bioplastics are not the solution
Β
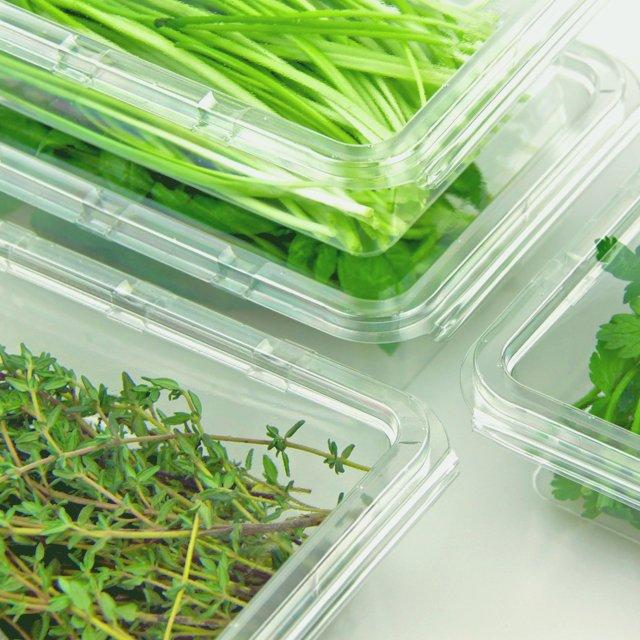
Any ideas on how to improve on this?
Voges is always open to new insights. If you have any ideas about how we could further optimise the production of our packaging, please let us know. We will always respond.
Contact